Industrial Racking: 5 Game-Changing Strategies for Optimised Warehouse Performance
- Lauren Bracy
- Mar 6
- 4 min read
Updated: Mar 19
Industrial Racking is the backbone of modern warehouse operations, enabling businesses to maximize space, streamline workflows, and enhance safety. As supply chains grow more complex, optimizing your racking system isn’t just an option—it’s a necessity. With rising demand for faster order fulfillment and efficient inventory management, adopting innovative strategies for industrial racking can transform warehouse performance. Below, we explore five game-changing approaches to unlock productivity, reduce costs, and future-proof your storage infrastructure.
Why Industrial Racking Optimization Matters

Warehouses often start with basic layouts, only to realize later that disorganized racking systems lead to wasted space and increased handling times. Cluttered aisles or underused vertical zones slow down workflows and strain employees. Optimizing your industrial racking isn’t just about storage—it’s about adaptability. For instance, seasonal demand spikes or new product lines require flexible configurations to avoid costly overhauls. Efficient designs also reduce physical strain on workers, lower labor costs, and improve inventory flow.
Compliance with Australian safety standards, such as AS 4084, becomes easier with a well-organized system. Meeting these guidelines isn’t just about avoiding penalties—it ensures daily operations run smoothly without unnecessary risks. A streamlined warehouse also keeps businesses competitive, as faster order fulfillment and adaptable layouts respond swiftly to market changes.
Key Challenges in Warehouse Space Utilization
Balancing current needs with future growth is a common hurdle. Seasonal surges or unexpected bulk orders can overwhelm existing systems, forcing rushed adjustments like narrowing aisles. However, cramped pathways risk forklift accidents, damaged goods, and workflow bottlenecks. Permanent solutions, such as mezzanine floors, may backfire if inventory patterns shift.
The first step to improvement is identifying underused areas. Are corners empty? Are vertical spaces ignored? Auditing your warehouse reveals quick fixes, like repositioning high-demand items closer to packing zones or adding modular shelving. Strategic planning for every square meter ensures safety and compliance while maximizing capacity.
Mastering Industrial Racking: Key Fundamentals for Warehouse Success
Industrial racking systems form the backbone of efficient warehouse operations, directly influencing workflow, safety, and profitability. Choosing the right setup can reduce labor costs, streamline processes, and enhance employee satisfaction. Here’s a breakdown of core principles to optimize your industrial racking strategy.
Types of Industrial Racking Systems
Selecting the right racking system depends on your inventory and workflow:
Selective Racking: Ideal for quick access to diverse SKUs, perfect for fast-moving goods like retail products.
Drive-In Racking: Maximizes storage density by allowing forklifts to enter lanes, suited for bulk items with low turnover.
Cantilever Racking: Designed for long, bulky items (e.g., timber, pipes), offering unobstructed loading.
Double-Deep Racking: Doubles storage depth but requires specialized forklifts, ideal for high-volume, uniform pallets.
Safety and Compliance in Australia
Australian warehouses must adhere to strict standards like AS 4084 for steel racking. Compliance involves proper load ratings, regular inspections, and maintenance to prevent accidents. Cutting corners risks penalties, operational shutdowns, or workplace injuries. Schedule routine audits and prioritize repairs to ensure systems meet safety benchmarks.
Common Warehouse Challenges
Avoid these pitfalls to maintain efficiency:
Poor Layouts: Narrow aisles or disorganized racks slow operations and increase forklift collision risks.
Outdated Systems: Damaged beams or mismatched racking lead to product damage and safety hazards.
Inadequate Labeling: Unclear signage wastes time and causes errors in inventory retrieval.
Tackling these issues early on not only prevents headaches but also creates a safer, more profitable workspace. By understanding the fundamentals, you set the stage for maximising space while minimising complications.
Optimizing Industrial Racking Systems: Practical Tips for Warehouse Efficiency
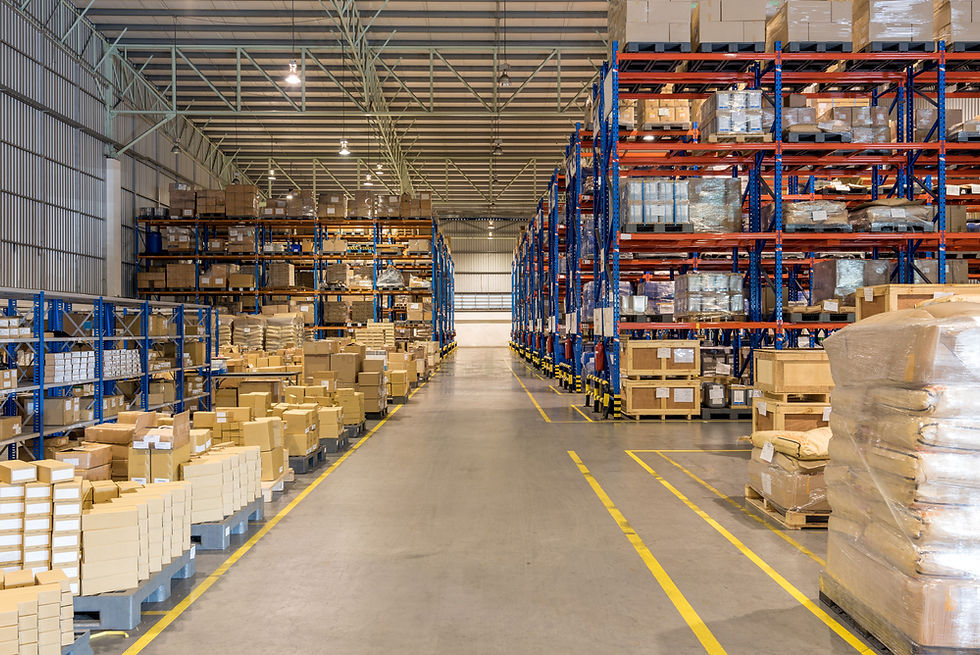
Industrial racking systems are the backbone of warehouse productivity, but many facilities struggle with wasted space, safety risks, and inefficient workflows. Below are actionable strategies to refine your setup, maximize storage, and align operations with business goals—all while keeping safety and compliance front and center.
Tip 1: Start with Quick, Low-Cost Fixes
Before investing in major upgrades, tackle “low-hanging fruit” for instant improvements:
Reorganize high-demand items: Place frequently picked goods near dispatch areas to cut retrieval time and reduce worker fatigue.
Label clearly: Use color-coded signage or bold labels to minimize errors and speed up inventory searches.
Utilize vertical space: Install extra beam levels or mezzanine shelving in underused overhead areas.
Audit idle zones: Walk through your warehouse to identify empty corners or half-empty racks. Staff input often reveals overlooked inefficiencies.
Tip 2: Design for High-Traffic Zones
Busy aisles and fast-moving stock require strategic planning:
Widen main aisles: Ensure forklifts can maneuver safely to avoid collisions and delays.
Prioritize fast-moving goods: Position high-turnover items near shipping docks. Flow racking systems, where items roll forward as picked, streamline fulfillment.
Seasonal flexibility: Use adjustable beams or temporary racks to handle peak demand without permanent changes.
Tip 3: Invest in Scalable Upgrades
Focus on upgrades that solve specific problems and grow with your needs:
Heavy-duty racking: Switch to adjustable or reinforced systems if inventory shifts to bulkier items.
Phased implementation: Upgrade one warehouse section at a time to manage costs and refine strategies.
Automation: Consider automated storage solutions to reduce labor costs and improve accuracy in high-volume operations.
Tip 4: Align Layouts with Business Goals

Your industrial racking system should directly support commercial objectives:
Speed-focused layouts: If quick delivery is a priority, place premium products near exits for rapid dispatch.
Flexible configurations: Use modular racks to accommodate seasonal shifts or new product lines.
Profit-driven zoning: Group high-margin items in easily accessible areas to accelerate order fulfillment.
Tip 5: Prioritize Maintenance and Safety
Even the best racking systems fail without proper care:
Monthly inspections: Check for bent beams, rust, or overloading. Annual professional audits are mandatory under Australian standards (AS 4084).
Train staff: Teach proper loading techniques and enforce weight limits to prevent damage.
Act on red flags: Swaying racks, loose bolts, or sagging shelves require immediate attention to avoid collapses.
Conclusion
A streamlined industrial racking system boosts warehouse productivity and safety. Start with quick fixes like reorganizing high-turnover items and using vertical space. Invest in scalable upgrades (adjustable racks, automation) for long-term gains. Prioritize regular inspections and staff training to meet Australian safety standards. Align layouts with business goals—position high-margin items strategically. A well-planned industrial racking setup isn’t just storage—it’s a competitive edge.
Comentarios