How Military Seals Improve Corrosion Resistance in MS Fasteners?
- David Fenton
- Mar 6
- 4 min read
Have you ever wondered why some metal fasteners last for decades, while others seem to rust away in no time? Or perhaps you’ve seen a fastener holding firm on an Australian naval vessel, even when exposed to salty sea spray day in and day out. These scenarios might spark your curiosity about how high-performance coatings defend against corrosion. If you’re keen to learn more about the secret behind resilient, long-running fasteners, you’re in the right place.
In this blog post, we’ll uncover how military seals enhance the corrosion resistance of MS fasteners. We’ll also explore their unique design features, why they’re so crucial in coastal environments, and how they measure up against other finishes like black oxide or zinc. Along the way, we’ll discuss marine-grade bolts, and automotive fastener coatings, and highlight the best coating for nuts and bolts exposed to all sorts of tough conditions.
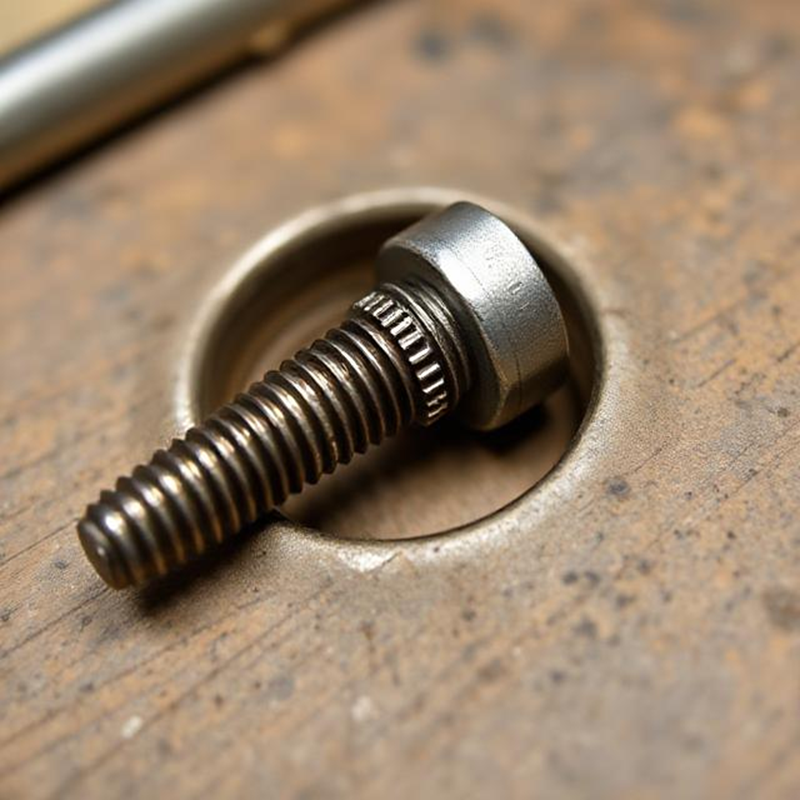
Fundamentals of Corrosion Resistance
What Causes Metal Corrosion?
Corrosion is essentially a chemical process triggered by the interaction of metal with oxygen and other substances—often moisture or salts. Once metal starts corroding, the process can accelerate under certain conditions. For instance, pitting corrosion occurs when a small flaw or crack allows moisture to penetrate, leading to localised damage. Over time, this can undermine a metal component’s strength.
How Coatings and Seals Protect Against Corrosion
Coatings and seals work by blocking environmental elements such as water, salt, and chemicals from touching the metal surface. Traditional finishes like zinc plating create a physical barrier that delays rust formation, while black oxide relies on a controlled treatment to give the metal a protective surface. Automotive fastener coatings often involve galvanisation or electroplating that maintains a sleek look and guards against rust.
Seals, on the other hand, go one step further. They typically feature special formulations designed to fill any tiny gaps or micro-pores. This reduces the risk of moisture slipping past the coating. Military seals are especially advanced, delivering higher durability and better adhesion. When used correctly, they keep fasteners in tip-top shape, even under aggressive conditions like saltwater immersion or chemical exposure.
Military Seals: The Ultimate Protective Layer
Unique Properties of Military-Grade Seals
Military-grade seals aren’t just your regular topcoat. They are state-of-the-art formulations built to handle harsh operational environments. These seals fuse advanced polymers, resins, or ceramic particles, making them both flexible and remarkably strong. They’re able to maintain adhesion despite constant vibration, temperature swings, and contact with corrosive substances.
Military Seals vs Standard Protective Finishes
What is the difference between standard finishes and military seals? Often, it comes down to the level of protection. Standard finishes like black oxide or zinc plating do create barriers, but they might not stand up to extreme conditions over extended periods. Military seals rely on multiple layers or advanced chemistry to gain robust corrosion resistance.
Why Military Seals Matter in Australian Coastal Environments
Australian coasts are known for their intense salt content and high humidity levels. Over time, the combination of sun, sand, and salt can damage standard fasteners, leading to rust. This risk is even higher when structures stand exposed to waves, storms, and wind-carrying corrosive salt particles.

Fastener Design Considerations
Importance of the Fastener Design Manual
A fastener design manual offers structured guidelines to help engineers pick the right type of bolt, screw coating, or surface finish. Whether you’re referencing a standard text or a specialised fastener design manual, these resources detail material used in military seals, torque requirements, and best practices.
Insights from the NASA Fastener Design Manual
The NASA Fastener Design Manual is among the most highly regarded references for threaded fasteners. It delves into torque calculations, load distribution, and how certain coatings affect friction. Although NASA’s focus is aerospace applications, many lessons apply to everyday industries.
How to Choose the Right Screw Coating?
Deciding on the perfect coating involves balancing factors like budget, environmental conditions, and performance expectations. For instance, in automotive manufacturing, you might lean towards zinc-based coatings due to their track record in road salt defence. A maritime project, on the other hand, might need stainless steel combined with a military seal.
How Military Seals Are Applied?
Preparing Fasteners for Sealing
Before any seal is applied, fasteners must be thoroughly cleaned and prepped. This includes removing any dirt, oil, or rust that might undermine the seal’s adherence. Techniques such as sandblasting, chemical baths, or ultrasonic cleaning help get rid of all residues.
Once surfaces are cleaned, they’re often inspected for micro-cracks or surface flaws that could allow moisture to sneak underneath the seal. Addressing these imperfections is vital for ensuring a smooth and reliable coating. Some processes also involve applying a primer coat to further enhance the seal’s bond.
Application Methods and Common Pitfalls
Military seals can be applied using spray booths, dip-spin processes, or electrostatic techniques. Each method has pros and cons. For instance, dip-spin might provide quick and uniform coverage but can lead to small drips if not carefully managed. Electrostatic painting can achieve a more even coat, though it requires more complex equipment.
Testing and Maintaining Military-Sealed Fasteners
After application, these fasteners are often tested using methods like salt spray or cyclical corrosion testing. This process checks the seal’s integrity under repeated exposure to reactive chemicals, moisture, and temperature shifts. If they pass with flying colours, they’re ready for use in tough environments.
However, proper maintenance must follow installation. Even military seals can degrade if hit with severe mechanical stress, chemical spills, or poor handling. Regular checks for chipping or cracking will help you spot issues early. Set up a scheduled inspection plan in corrosive environments to ensure the fasteners keep their protective properties over time.

Conclusion
Ultimately, the next time you’re choosing military seals in fasteners for a coastal or industrial project, remember the difference that a properly applied military seal can make. Aim for top-quality materials, advanced finishes, and proven standards, and you’ll set yourself up for success. With so many options available—black oxide screws vs stainless steel, black phosphate coating vs zinc, or respect coating vs stainless steel—military sealing offers a degree of reassurance that’s hard to beat. When corrosion resistance is a must-have, a military seal might well be the deciding factor.
Comments